Contents
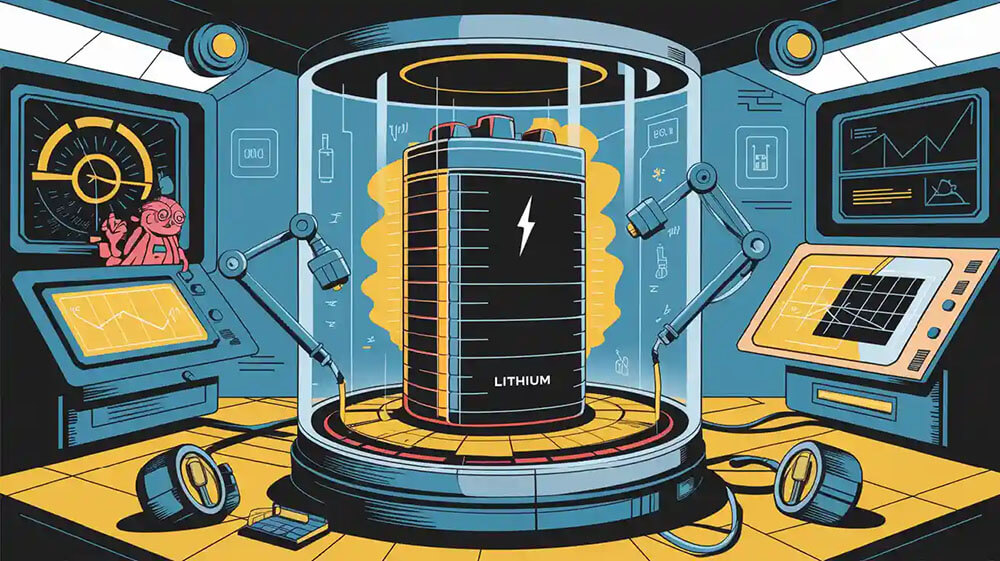
Low-pressure testing examines how a lithium battery functions under reduced atmospheric conditions. This evaluation is essential to ensure the safety and reliability of lithium batteries in environments like high altitudes or vacuum-like settings. Such testing is particularly critical for industries like aerospace, where devices face extreme altitudes, and for underwater equipment, which operates in pressurized environments.
Key Takeaways
Low-pressure testing checks if lithium-ion batteries are safe for flying. It mimics high-altitude air to lower risks like overheating.
Following UN38.3 rules is important for these batteries. It proves they stay stable in low pressure and allows worldwide use.
Adding low-pressure tests during design makes batteries safer and stronger. This helps stop problems like leaks or fires in tough conditions.
Part 1: Purpose of Low-Pressure Testing for Lithium Battery
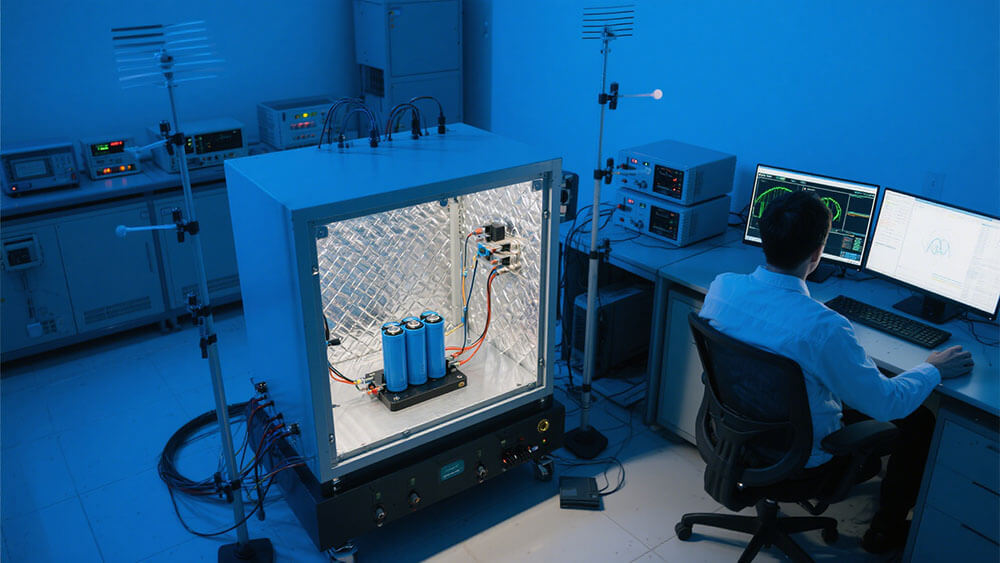
1.1 Ensuring Safety During Air Transport
Lithium-ion batteries are widely used in portable electronics, medical devices, and aerospace applications. However, transporting these batteries by air poses unique challenges due to the reduced atmospheric pressure at high altitudes. Low-pressure testing ensures that lithium-ion batteries can withstand these conditions without compromising safety.
During air transport, the risk of thermal runaway—a chain reaction that can lead to overheating, fire, or explosion—becomes a critical concern. Low-pressure testing helps mitigate this risk by simulating high-altitude conditions and evaluating battery performance. For example:
Reducing the state of charge in lithium-ion batteries decreases the likelihood of thermal runaway.
It prevents thermal runaway from spreading to adjacent cells or batteries.
It enhances the battery’s ability to tolerate short circuits and reduces the maximum temperature during such events.
It minimizes the release of gases and the heating rate if thermal runaway occurs.
Historical incidents underscore the importance of this testing. In 2006, a fire linked to lithium-ion batteries destroyed a cargo aircraft in Philadelphia. Similar tragedies occurred in Dubai (2010) and international waters (2011), highlighting the need for rigorous safety measures. By conducting low-pressure testing, you can ensure that your lithium-ion batteries meet the safety requirements for air transport, reducing the risk of fire and explosion.
1.2 Compliance with UN38.3 Testing Standards
Compliance with UN38.3 testing is mandatory for lithium-based batteries before they can be transported. These standards, enforced by the United Nations Economic Commission for Europe (UNECE), ensure that batteries are safe for various transportation methods, including air, sea, and land.
Low-pressure testing is a critical component of UN38.3. It involves simulating air transport conditions to verify that the battery remains stable under low air pressure. The test, known as T.1 Altitude Simulation, evaluates whether the battery exhibits any mass loss, leakage, venting, disassembly, rupture, or fire. Additionally, the battery’s voltage must remain at least 90% of its pre-test value.
Test | Purpose | Test Procedure | Requirement |
---|---|---|---|
T.1 | Altitude simulation | Simulates air transport under low-pressure conditions. | No mass loss, leakage, venting, disassembly, rupture, or fire; voltage must be at least 90% of pre-test voltage. |
Adhering to these standards not only enhances safety but also facilitates global market access. Manufacturers who comply with UN38.3 can distribute their products internationally without facing regulatory hurdles. This compliance also supports the development of safer battery designs, reducing the risk of thermal runaway and other hazards.
1.3 Preventing Hazards in Low-Pressure Environments
Low-pressure environments, such as those encountered in aerospace or high-altitude operations, can amplify the risks associated with lithium-ion batteries. Without proper testing, these batteries may experience pressure-induced failures, leading to safety risks like leakage, venting, or even fire and explosion.
Low-pressure testing serves as an essential environmental safety test to identify and mitigate these risks. By simulating conditions such as reduced pressure, temperature cycling, and altitude changes, this testing ensures that lithium-ion batteries can perform reliably in challenging environments. Numerical studies have shown that pressure variations significantly impact hazard reduction. For instance, experiments using FDS software revealed how peak pressure sensitivity to leakage areas could influence safety outcomes.
By incorporating low-pressure testing into your battery development process, you can design lithium-ion battery packs that are more resilient to environmental stressors. This not only enhances safety but also aligns with industry standards and testing requirements, ensuring that your products meet the highest levels of reliability and performance.
For more information on how to customize lithium-ion battery solutions for specific applications, visit Large Power’s Custom Battery Solutions.
Part 2: Low-Pressure Testing Process for Lithium-Ion Battery
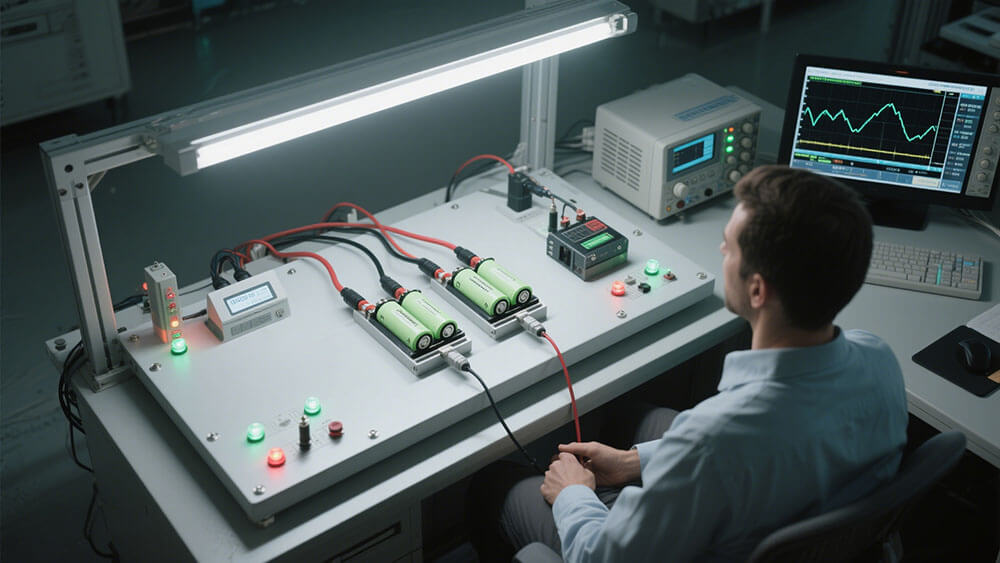
2.1 Testing Procedures and Protocols
Low-pressure testing for lithium-ion batteries involves a series of carefully designed procedures to evaluate their performance and safety under reduced atmospheric conditions. You must follow strict protocols to ensure accurate and reliable results. These protocols typically align with international standards, such as UN38.3, which mandate specific testing requirements for lithium-based batteries.
The process begins with preparing the battery samples. Each sample undergoes pre-test inspections to confirm its physical integrity and initial voltage levels. Once prepared, the batteries are placed in a specialized test chamber that simulates low air pressure conditions. The chamber gradually reduces the pressure to replicate altitudes of up to 100,000 feet above sea level. During this phase, you monitor the battery for any signs of leakage, venting, or structural failure.
After the pressure simulation, the batteries are subjected to additional evaluations, such as temperature cycling and overcharge tests. These tests assess the battery’s ability to withstand rapid temperature changes and electrical stress. The final step involves post-test inspections to measure voltage retention and identify any physical or chemical changes. By adhering to these procedures, you can ensure that your lithium-ion batteries meet the highest safety and performance standards.
2.2 Equipment Used in Environmental Safety Tests
The success of low-pressure testing depends on the use of advanced equipment designed to replicate challenging environmental conditions. These devices play a crucial role in ensuring the accuracy and reliability of the test results.
Specification | Description |
---|---|
Test Type | Low Pressure Altitude Test |
Application | Aviation, Aerospace, Military, Electronics |
Pressure Range | Up to 100,000 feet above sea level |
Purpose | Evaluate equipment performance under low air pressure conditions |
Test Conditions | High/low temperature with reduced air pressure |
The test chamber is the centerpiece of the setup. It simulates high-altitude conditions by creating a controlled environment with reduced air pressure. This chamber also allows you to introduce temperature variations, enabling comprehensive thermal tests. Additional equipment includes voltage monitors, thermal sensors, and gas analyzers. These tools help you detect potential hazards, such as thermal runaway or gas venting, during the testing process.
Using this equipment, you can assess the impact of rapid pressure drops on lithium-ion batteries. For example, the test machine evaluates how the battery’s internal components respond to sudden changes in pressure and temperature. This data is invaluable for designing safer and more reliable lithium-ion battery packs for critical applications.
2.3 Simulated Conditions: Altitude, Pressure, and Temperature
Low-pressure testing involves recreating the environmental conditions that lithium-ion batteries may encounter during their lifecycle. These simulated conditions include altitude, pressure, and temperature, which are critical factors affecting battery performance and safety.
Altitude simulation replicates the low air pressure experienced at high altitudes, such as during air transport or aerospace operations. The test chamber reduces the pressure to levels equivalent to altitudes of up to 100,000 feet. This simulation helps you identify potential risks, such as leakage or structural failure, that could lead to fire and explosion.
Temperature cycling is another essential aspect of the testing process. Batteries are exposed to extreme temperature variations to evaluate their thermal stability. For instance, a thermal test may involve alternating between high and low temperatures while maintaining reduced air pressure. This approach ensures that the battery can withstand the combined stress of temperature and pressure changes.
By simulating these conditions, you can gain valuable insights into the performance and durability of lithium-ion batteries. This information is crucial for meeting testing requirements and ensuring compliance with international safety standards. It also supports the development of robust battery designs that can operate reliably in demanding environments.
For more information on customizing lithium-ion battery solutions for specific applications, visit Large Power’s Custom Battery Solutions.
Part 3: Significance of Environmental Safety Test Results
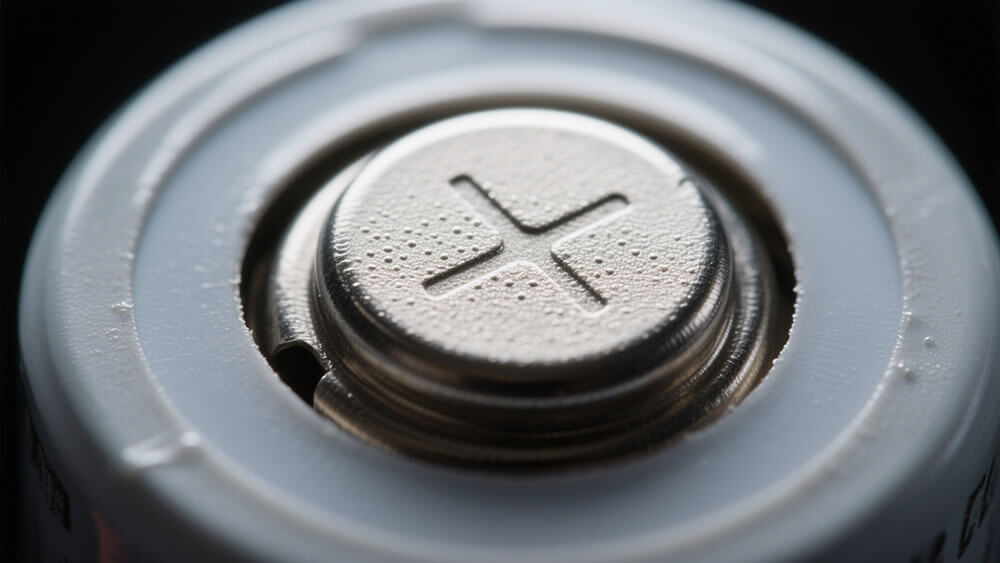
3.1 Enhancing Lithium-Ion Battery Safety and Reliability
Environmental safety testing plays a pivotal role in improving the safety and reliability of lithium-ion batteries. By simulating real-world conditions such as low air pressure, extreme temperatures, and rapid altitude changes, you can identify potential risks like thermal runaway or structural failure. These insights allow you to implement design modifications that enhance the battery’s resilience and performance.
For instance, low-pressure testing ensures that lithium-ion batteries can withstand the challenges of air transport and aerospace applications. It also helps you address critical safety concerns, such as gas venting and leakage, which could compromise the battery’s functionality. By integrating these tests into your development process, you can produce batteries that meet stringent safety standards and perform reliably in demanding environments.
3.2 Supporting Certification and Market Approval
Environmental safety tests are essential for achieving certification and gaining market approval for lithium-based batteries. These tests evaluate how batteries perform under extreme conditions, such as high humidity and temperature fluctuations. Meeting these testing requirements ensures that your batteries comply with international safety standards, such as IEC 62133, which outlines electrical, mechanical, and chemical safety protocols.
Environmental tests assess battery performance under extreme temperatures and humidity.
Compliance testing ensures adherence to transportation regulations and safety standards.
Certification processes, such as those outlined in IEC 62133, include rigorous evaluations for electrical and mechanical safety.
By meeting these requirements, you can streamline the certification process and expand your market reach. Certified lithium-ion batteries not only gain consumer trust but also align with global transportation and safety regulations, ensuring seamless distribution across industries.
3.3 Implications for Lithium-Ion Battery Pack Design
Low-pressure test results provide valuable data that inform the design of lithium-ion battery packs. For example, research shows a strong correlation between pack current and temperature rise, highlighting the importance of optimizing current flow to minimize heat generation.
Measurement Type | Correlation with Temperature Rise | Notes |
---|---|---|
Pack Current | Strong correlation | Current dependent losses |
Pack Voltage | No correlation | Voltage not a function of loss |
Filtered Current | Strong correlation | 1 mHz low-pass filter used |
Estimated Temp | Strong correlation | Based on LP thermal model |
By analyzing this data, you can refine your battery pack designs to improve thermal management and reduce the risk of overheating. These design enhancements not only improve safety but also extend the lifespan of lithium-ion batteries, making them more reliable for critical applications. To explore customized solutions tailored to your specific needs, visit Large Power’s Custom Battery Solutions.
Low-pressure testing plays a vital role in ensuring the safety and reliability of lithium-ion batteries. You can use this testing to evaluate how batteries perform under challenging conditions, such as reduced air pressure and extreme temperatures. These insights help you meet certification requirements, like UN38.3, and improve battery designs for critical applications.
By prioritizing low-pressure testing, you advance lithium-ion battery technology and ensure compliance with global safety standards. This approach supports safer transportation and reliable performance across industries.
FAQ
1. What is the purpose of low-pressure testing for lithium-ion batteries?
Low-pressure testing ensures battery safety and reliability in reduced atmospheric conditions, such as during air transport or aerospace operations.
2. How does low-pressure testing comply with UN38.3 standards?
It simulates air transport conditions to verify stability, preventing hazards like leakage, venting, or fire, and ensuring voltage retention above 90%.
3. Can low-pressure testing improve battery design?
Yes, it provides data on performance under stress, enabling you to refine designs for better thermal management and enhanced safety.
Tip: For professional guidance on low-pressure testing, visit Large Power.