Contents
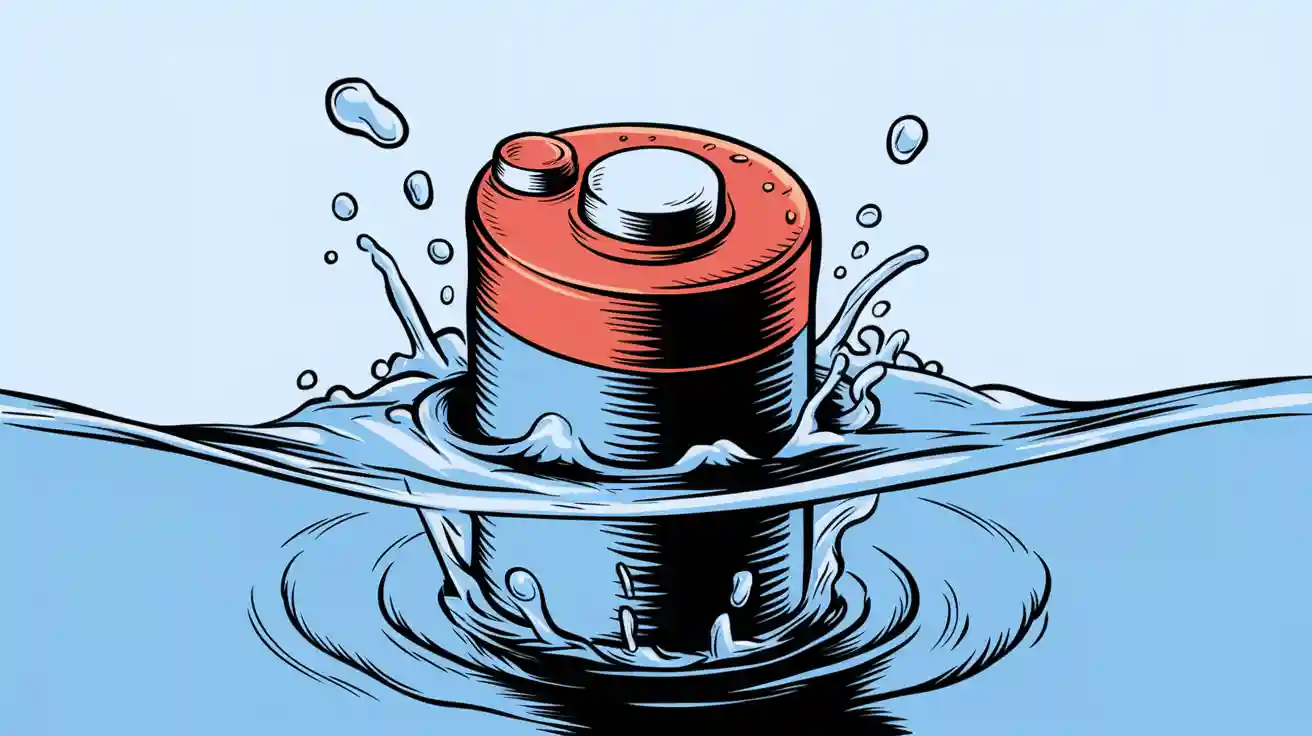
Lithium battery packs play a vital role in powering industrial equipment, outdoor devices, and consumer electronics. Understanding how batteries are waterproof is essential for protecting them from environmental hazards, such as moisture and dust, which can compromise safety and performance.
A waterproof rating like IP67 or IP68 ensures reliability under specific conditions. For instance, a rating of IP6X signifies complete dust-tight protection, while IPX7 or IPX8 indicates varying levels of water resistance.
The waterproof lithium battery market is growing rapidly, valued at USD 1.2 billion in 2024 and projected to reach USD 2.5 billion by 2033. This surge highlights the increasing demand for robust, long-lasting energy solutions in rugged applications.
Key Takeaways
Focus on making batteries waterproof when designing them for safety.
Use strong materials for covers and seals to block water.
Check and test often to keep them waterproof and spot issues early.
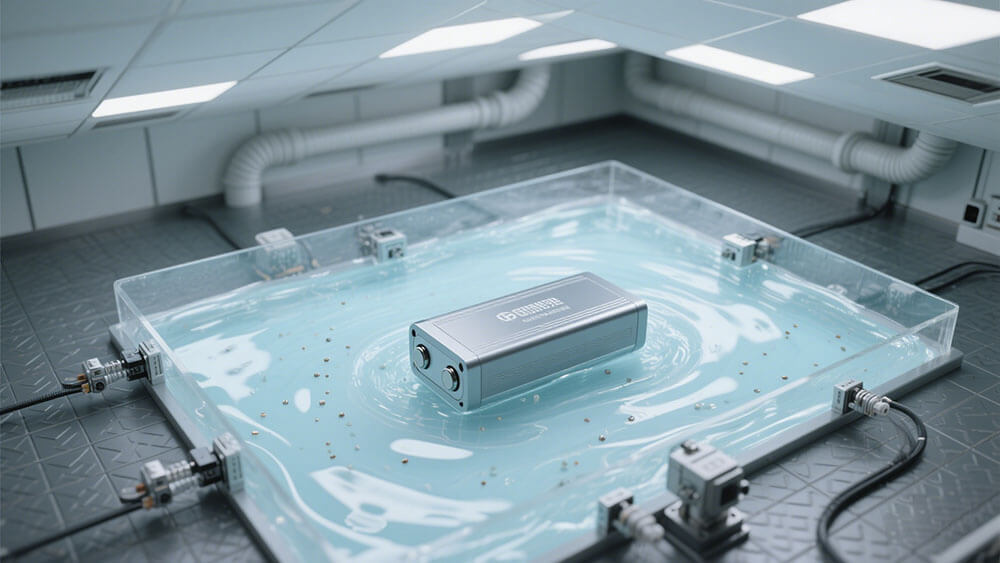
Part 1: How Batteries Are Waterproof During Design
1.1 Importance of Waterproofing in Battery Design
Waterproofing plays a critical role in ensuring the reliability and safety of lithium battery packs, especially in demanding applications like industrial equipment, consumer electronics, and robotics. Exposure to moisture can lead to short circuits, corrosion, or even catastrophic failures. By designing batteries with robust waterproofing measures, you can protect sensitive components and extend their lifespan.
In environments such as medical devices or security systems, where uninterrupted performance is vital, waterproofing becomes even more essential. For instance, batteries used in infrastructure applications like transportation must withstand harsh conditions, including rain, humidity, and dust. Incorporating waterproof designs ensures that your batteries remain functional and safe, regardless of external challenges.
Tip: Prioritize waterproofing during the design phase to avoid costly repairs or replacements later.
1.2 Material Selection for Casings and Seals
Choosing the right materials for casings and seals is fundamental to achieving waterproofing. High-performance materials like aluminum alloys, stainless steel, and engineering plastics offer excellent resistance to water ingress. Silicone-based sealants and gaskets provide additional protection by filling gaps and preventing leaks.
Material property tests help you evaluate the performance of casings and seals under stress. Key tests include:
Peak Force: Measures maximum seal strength, ensuring materials can withstand extreme conditions.
Average Peel Force: Assesses overall seal integrity, enabling comparisons across different materials.
Failure Mode Evaluation: Identifies failure types (adhesive, cohesive, or material-related) to optimize material selection.
Other tests, such as fluid aging and compression set evaluations, predict long-term performance. These tests allow you to statistically compare materials and select the most reliable options for your battery design.
Material | Properties | Applications |
---|---|---|
Aluminum Alloy | Lightweight, corrosion-resistant | Consumer electronics, robotics |
Stainless Steel | Durable, high tensile strength | Industrial equipment, infrastructure |
Engineering Plastics | Cost-effective, versatile | Medical devices, security systems |
1.3 Designing for IP67 and IP68 Standards
Achieving IP67 and IP68 standards ensures your batteries are protected against dust and water. IP67-rated designs can withstand short-term immersion in water, while IP68-rated designs offer protection for prolonged exposure. These ratings are based on the IEC 60529 standard, which outlines rigorous testing methods for dust and water resistance.
To meet these benchmarks, focus on:
Seamless Enclosures: Use ultrasonic welding or laser welding to eliminate gaps.
Seal Integrity: Apply high-quality gaskets and adhesives to prevent leaks.
Ventilation Solutions: Incorporate waterproof breathable membranes to balance internal pressure without compromising protection.
Understanding IP ratings allows you to select designs tailored to specific environments. For example, batteries used in underwater robotics or outdoor infrastructure require IP68 protection, while those in consumer electronics may only need IP67.
Note: Always verify your designs through immersion and spray tests to ensure compliance with IP standards.
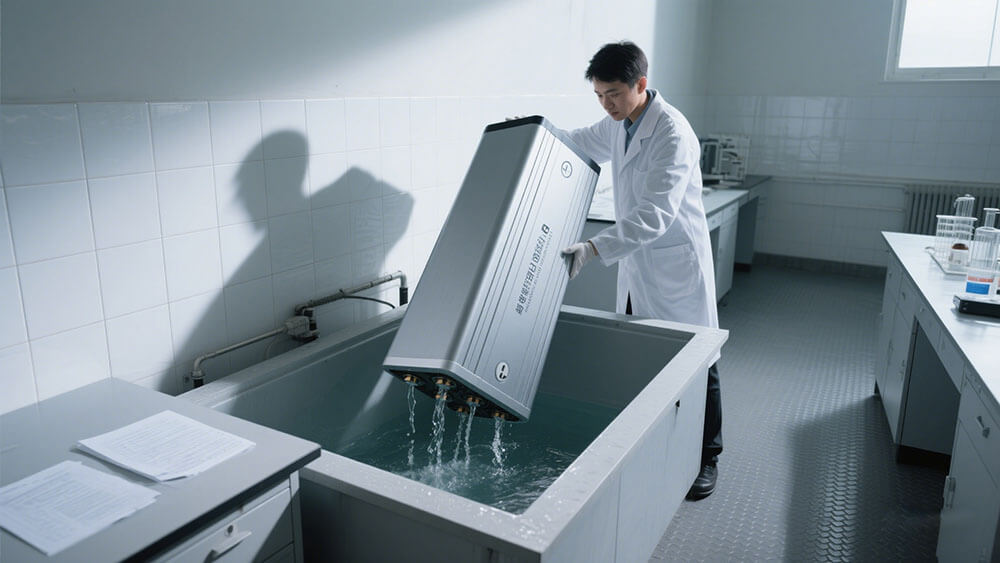
Part 2: Methods for Waterproofing Batteries
2.1 Applying Waterproof Coatings to Battery Components
Waterproof coatings serve as the first line of defense against moisture intrusion. These coatings create a hydrophobic barrier on battery components, preventing water from reaching sensitive areas. Advanced materials like Parylene and conformal coatings are commonly used due to their excellent dielectric properties and resistance to environmental stress.
Research demonstrates the effectiveness of waterproof coatings in enhancing battery durability. For instance, magnesium metal anodes protected by a hydrophobic and Mg2+-permeable interphase maintained stable cycling performance even after water exposure. Similarly, waterproof batteries have shown reliable performance in humid environments and saltwater immersion, maintaining stable open circuit voltage. These findings highlight the critical role of coatings in ensuring long-term reliability.
When applying waterproof coatings, ensure uniform coverage across all components. This step minimizes the risk of weak points where water could penetrate. Coatings also protect against dust, further contributing to how batteries are waterproof in challenging environments.
Tip: Regularly inspect coated surfaces for wear or damage to maintain optimal protection.
2.2 Using Sealants for Gaps and Connectors
Sealants play a crucial role in filling gaps and securing connectors, ensuring a watertight enclosure for your battery pack. Silicone-based sealants and epoxy adhesives are popular choices due to their flexibility, durability, and resistance to environmental factors.
Quantitative tests validate the performance of sealants in waterproofing applications:
Experiment Description | Observations | Conclusions |
---|---|---|
Sealant thickness measured at 3-mm | Gap filled with sealant | Sealants effectively fill gaps |
Localized sealant test with no visible emissions | No emissions detected where sealant applied | Sealants prevent emissions even when dry |
Gas leakage test with torch flame | No combustion in sealed areas | Sealants are gas-tight and effective against leakage |
These results confirm that sealants not only prevent water ingress but also enhance the overall structural integrity of the battery. For connectors, using high-IP-rated waterproof plugs ensures a secure and reliable connection.
Note: Apply sealants carefully to avoid over-application, which could interfere with heat dissipation.
2.3 Ultrasonic Welding for Seamless Enclosures
Ultrasonic welding is a cutting-edge method for creating seamless enclosures that enhance waterproofing. This technique uses high-frequency vibrations to fuse materials like plastics or metals, forming a strong, gap-free bond. Unlike traditional adhesives, ultrasonic welding eliminates the risk of sealant degradation over time.
This method is particularly effective in achieving IP67 and IP68 standards, as it ensures no water can penetrate the enclosure. For lithium-ion battery packs, ultrasonic welding provides a robust solution for applications in industrial and consumer electronics, where durability and reliability are paramount.
The process also supports sustainable manufacturing practices by reducing the need for additional materials like adhesives. Learn more about sustainability in battery design at Large Power.
Callout: Consider ultrasonic welding for high-performance applications requiring long-term waterproofing.
2.4 Potting and Encapsulation for Internal Protection
Potting and encapsulation involve filling the internal spaces of a battery pack with protective materials like epoxy resin or silicone gel. This method provides dual benefits: it prevents water ingress and enhances structural stability.
Encapsulation materials also improve thermal management by dissipating heat more effectively. This feature is particularly beneficial for high-capacity lithium-ion batteries used in robotics and infrastructure applications. By eliminating air gaps, potting materials reduce the risk of condensation, further contributing to how batteries are waterproof.
Potting compounds must be carefully selected to balance waterproofing with other performance factors. For example, thermally conductive materials can enhance heat dissipation, while flexible compounds accommodate expansion and contraction during operation.
Tip: Use potting materials compatible with your battery chemistry to avoid adverse reactions.
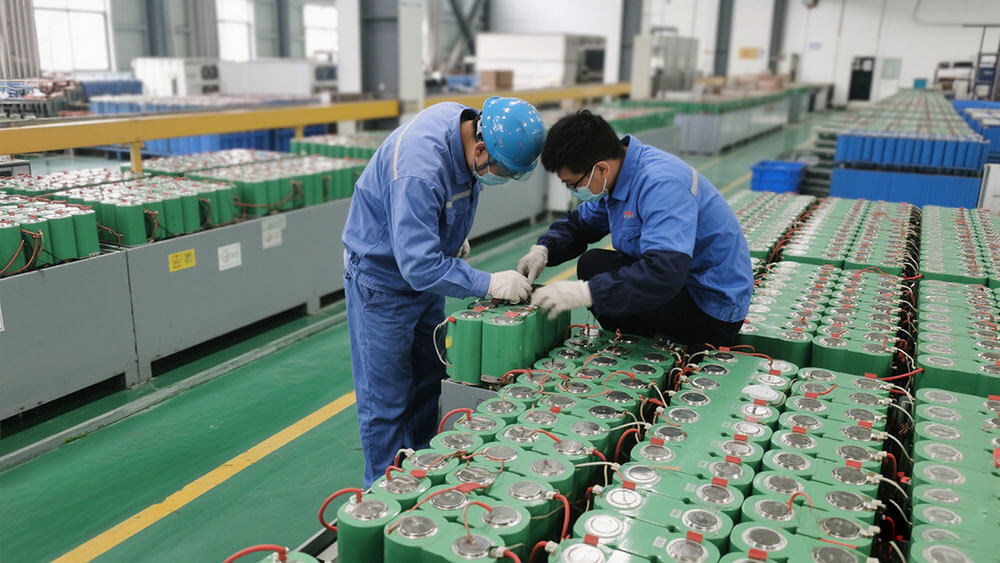
Part 3: Testing and Verification of Waterproofing
3.1 Conducting Immersion and Spray Tests
Testing waterproofing through immersion and spray tests ensures your battery’s reliability in wet environments. These tests simulate real-world conditions to evaluate how well the battery resists water ingress. Common methods include:
Submersion Testing: The battery is submerged in water for a specified duration to assess its resistance to water penetration.
Spray Testing: A Rain Spray Test Chamber replicates rainfall conditions, allowing you to measure the battery’s performance under simulated rain exposure.
Drip Testing: This method evaluates the battery’s ability to withstand water dripping from above, mimicking scenarios like condensation or light rain.
Advanced systems, such as the JL-X waterproof test system, provide precise immersion testing using devices like the JL-7 and JL-8. These tests help you verify compliance with IP67 or IP68 standards, ensuring your battery remains functional in challenging environments.
Tip: Always conduct these tests under controlled conditions to obtain accurate and reliable results.
3.2 Air Pressure and Leak Detection Tests
Air pressure and leak detection tests are essential for identifying potential weak points in your battery’s waterproofing. These tests involve pressurizing the battery casing and monitoring for pressure drops, which indicate leaks.
A common approach is the gas leakage test, where a sealed battery is exposed to a torch flame. If no combustion occurs, the seal is confirmed to be airtight. This method ensures that your battery’s enclosure can withstand environmental stress without compromising its integrity.
Leak detection tests are particularly useful for verifying the performance of sealants and gaskets. By identifying vulnerabilities early, you can address them before deploying the battery in critical applications like robotics or infrastructure.
Callout: Regularly perform leak detection tests to maintain the long-term reliability of your waterproof batteries.
3.3 Evaluating Long-Term Durability of Seals
The durability of seals plays a crucial role in maintaining waterproofing over time. Repeated immersion cycles and exposure to environmental factors can degrade sealants, leading to potential failures. Testing protocols simulate these conditions to evaluate seal performance.
Aspect | Description |
---|---|
Testing Method | Exposes seals to artificial weathering and cyclic movement. |
Purpose | Simulates natural weathering effects on waterproofing materials. |
Limitations | Does not account for localized conditions like pollution or biological attack. |
Variability | Results depend on parameters like temperature and movement amplitude. |
Applicability | Correlation with real-world conditions requires careful interpretation. |
These tests help you predict how seals will perform under prolonged use. For example, batteries used in outdoor infrastructure or industrial applications must endure harsh conditions without compromising their waterproofing.
Note: Choose high-quality sealants and conduct regular inspections to ensure consistent performance.
Part 4: Precautions and Maintenance for Waterproof Batteries
4.1 Regular Inspection of Seals and Casings
Regular inspections are essential for maintaining the waterproof integrity of lithium battery packs. Over time, seals and casings can degrade due to environmental exposure or mechanical stress, increasing the risk of water ingress. You should implement a structured maintenance program to identify and address potential vulnerabilities before they lead to failures.
Modern condition-based monitoring (CBM) technologies can enhance your inspection process. These include:
Vibration Monitoring: Detects structural weaknesses in casings.
Thermography: Identifies temperature anomalies that may indicate seal degradation.
Ultrasonic Testing: Pinpoints micro-leaks in seals and connectors.
Incorporating preventive maintenance (PM) and predictive maintenance (PdM) practices ensures consistent performance. For example, periodic testing and visual inspections can help you detect early signs of wear, while advanced CBM tools provide real-time data to predict potential issues.
Tip: Schedule inspections based on the battery’s operating environment. Batteries used in industrial applications, such as robotics or infrastructure, may require more frequent checks due to harsher conditions.
4.2 Avoiding Extreme Environmental Conditions
Extreme environmental conditions can compromise the waterproofing of your battery pack. High temperatures, prolonged submersion, or exposure to corrosive substances can weaken seals and degrade protective coatings. To mitigate these risks, you should take proactive measures to safeguard your batteries.
Temperature Management: Use thermally conductive materials or cooling systems to prevent overheating.
Controlled Environments: Store batteries in dry, temperature-regulated spaces when not in use.
Protective Barriers: Apply additional coatings or housings for batteries exposed to saltwater or industrial chemicals.
For outdoor applications, such as infrastructure or consumer electronics, consider IP68-rated designs that offer enhanced protection against prolonged water exposure. Additionally, avoid subjecting batteries to high-pressure water jets or extreme humidity, as these conditions may exceed their design limits.
Callout: Consult with experts to customize your battery solutions for specific environments. Explore custom battery solutions to ensure optimal performance and durability.
Waterproofing lithium battery packs demands careful design, advanced materials, and thorough testing. By implementing proper methods and regular maintenance, you can enhance battery performance and longevity in challenging environments.
Tip: Always choose professional-grade solutions and follow industry standards to ensure safety and reliability. This approach protects your investment and ensures optimal results.
FAQ
1. What is the difference between IP67 and IP68 waterproof ratings?
IP67 protects against short-term water immersion, while IP68 offers protection for prolonged submersion. Choose based on your battery’s intended application and environmental exposure.
2. How often should you inspect waterproof batteries?
Inspect seals and casings every 6-12 months. For harsh environments, increase inspection frequency to ensure long-term reliability and performance.
Tip: For professional guidance on waterproof batteries, visit Large Power.
3. Can waterproof batteries withstand saltwater exposure?
Yes, but only if designed for it. Use IP68-rated batteries with corrosion-resistant materials and additional protective coatings for saltwater environments.