Contents
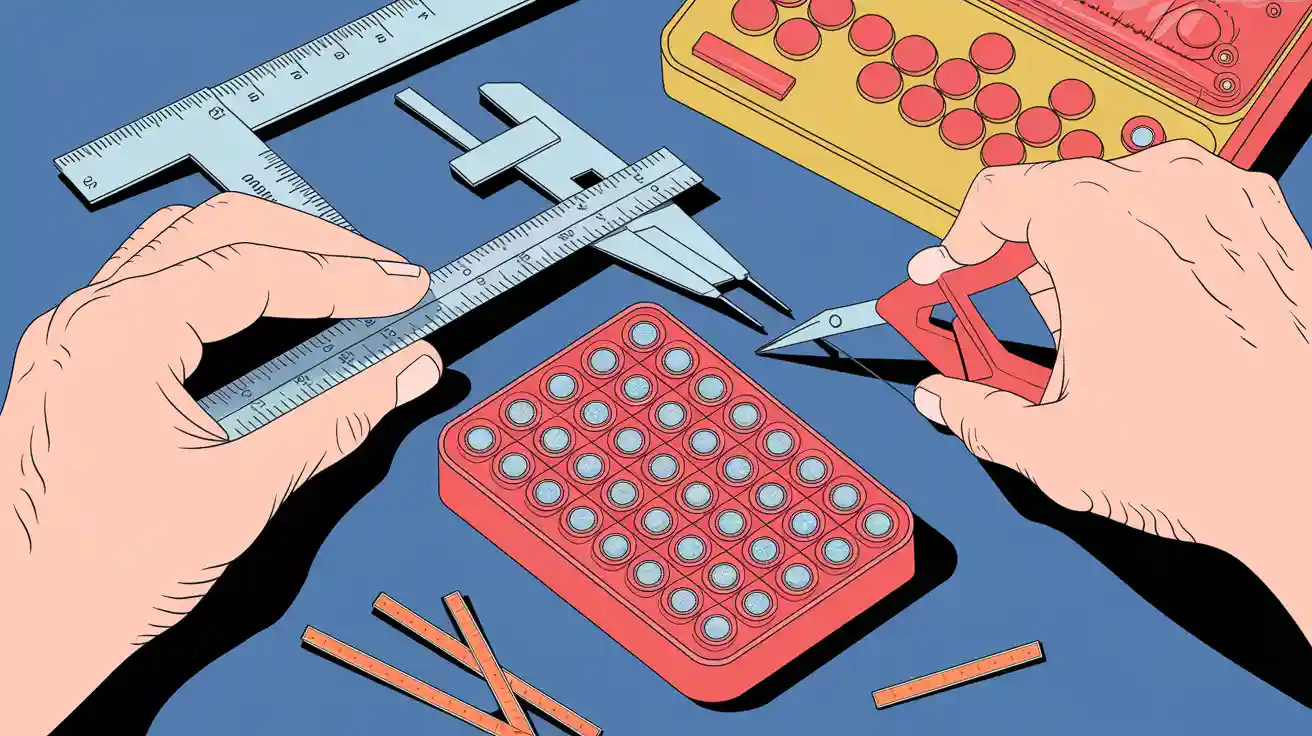
Properly sizing nickel strips for batteries is essential for ensuring both performance and safety. These strips connect the anodes and cathodes within battery cells, enabling efficient energy transfer. A standard size, such as 4 mm, is often used to optimize conductivity and minimize overheating risks. Without the correct dimensions, energy loss and thermal issues may compromise your battery pack’s reliability.
Key Takeaways
Correct nickel strip size improves battery safety and performance. Pick common sizes like 4 mm to boost energy flow and avoid overheating.
Choose pure nickel strips for important uses. They conduct electricity well and resist rust, making them strong and dependable.
Check how much current nickel strips can handle to stop overheating. Use thicker or wider strips to spread current and keep temperatures safe.
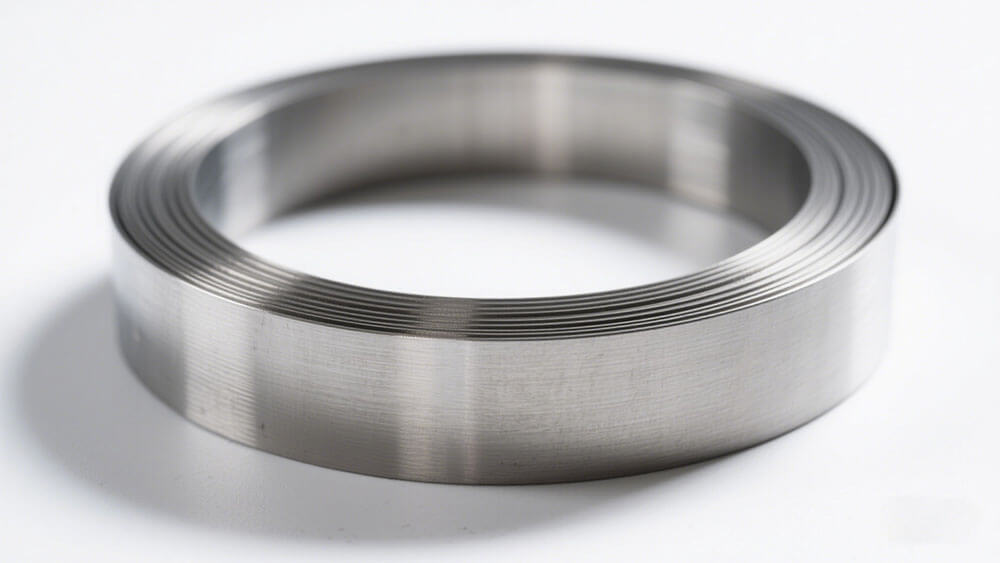
Part 1: What Are Nickel Strips for Battery Packs?
1.1 The role of nickel strips in lithium battery packs
Nickel strips play a critical role in lithium battery packs by serving as conductive pathways between individual cells. These strips ensure that energy flows efficiently from one cell to another, enabling the battery pack to deliver consistent power output. Without properly sized nickel strips, the battery pack may experience uneven energy distribution, leading to performance issues or overheating.
Historically, nickel strips have been integral to the development of advanced battery technologies. For example, nickel-hydrogen batteries, introduced in the early 1980s, relied on nickel components for energy storage in communication satellites. Similarly, nickel-metal hydride (NiMH) batteries, launched in 1989, utilized nickel strips for their durability and extended lifespan. The table below highlights key milestones in the evolution of nickel-based battery technologies:
Battery Type | Year Introduced | Key Features |
---|---|---|
Nickel–hydrogen battery | Early 1980s | Used in communication satellites as an energy-storage subsystem. |
Nickel–metal hydride (NiMH) | 1989 | Consumer-grade batteries with longer lifespans than NiCd batteries. |
Nickel strip specifications | N/A | Current capacity calculations for battery packs to prevent overheating. |
1.2 Benefits of nickel strips for energy transfer and durability
Nickel strips offer several advantages for energy transfer and durability in battery packs. Their high conductivity ensures minimal energy loss during operation, which is essential for applications like medical devices, robotics, and consumer electronics. Additionally, nickel strips are highly resistant to corrosion, making them ideal for long-term use in demanding environments.
Another benefit is their ability to handle high current loads without significant heat generation. This feature reduces the risk of thermal runaway, a critical safety concern in lithium-ion battery packs. By using nickel strips, you can enhance the overall reliability and lifespan of your battery pack, ensuring optimal performance across various applications.
For custom battery solutions tailored to your specific needs, consider consulting experts at Large Power.
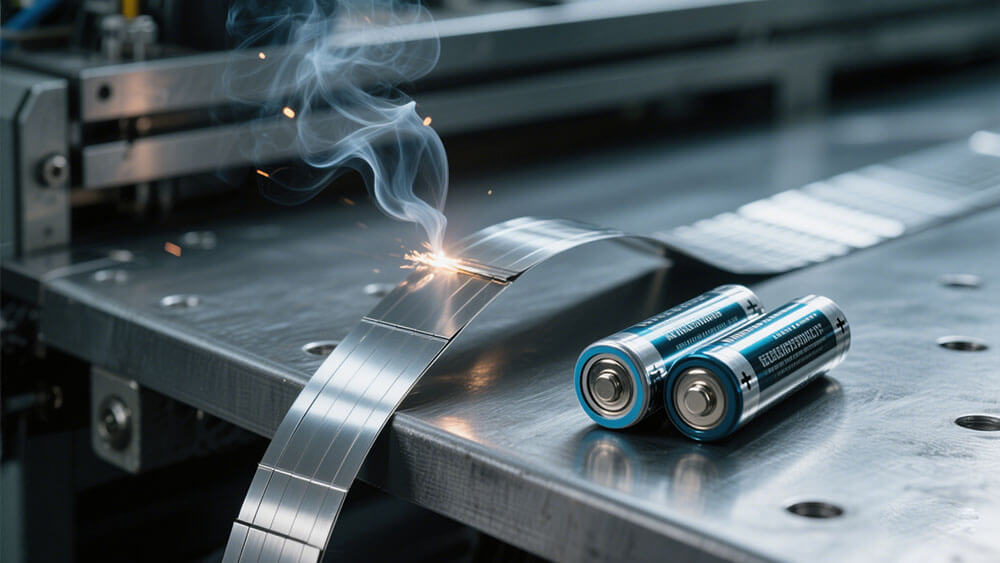
Part 2: Key Factors in Sizing Nickel Strips for Batteries
2.1 Determining the right thickness and width for your battery pack
The thickness and width of nickel strips are critical for ensuring the efficiency and safety of your battery pack. These dimensions directly influence the strip’s ability to carry current without overheating or causing energy loss. A thicker strip can handle higher currents, while a wider strip increases the surface area for electrical contact, reducing resistance and heat generation.
For example, industry standards suggest that a 0.15 mm thick nickel strip can carry up to 17 A of current. However, if your battery management system (BMS) requires a continuous discharge current of 40 A, you would need multiple layers of nickel strips to distribute the load effectively. Using the formula for resistance calculation:
Resistance = Length / (Width × Thickness) × Bulk Resistivity
you can determine the optimal dimensions for your application. For a strip with a length of 50 mm, width of 14 mm, and thickness of 0.15 mm, the resistance would be approximately 0.001664 ohms when carrying 40 A. This results in a voltage drop of 0.0666 V, which is within acceptable limits for most lithium-ion battery packs.
Tip: Always consider the power loss (calculated as I² × R) when selecting the thickness and width of your nickel strips. This ensures your battery pack operates efficiently without unnecessary heat buildup.
2.2 Material selection: Pure nickel vs. nickel-plated steel
Choosing the right material for your nickel strips is just as important as determining their dimensions. Pure nickel strips are highly conductive and resistant to corrosion, making them ideal for applications requiring long-term durability. In contrast, nickel-plated steel strips are more affordable but have higher resistance and are prone to corrosion over time.
Material Type | Conductivity | Corrosion Resistance | Cost | Best Use Cases |
---|---|---|---|---|
Pure Nickel | High | Excellent | Higher | |
Nickel-Plated Steel | Moderate | Moderate | Lower | Low-cost consumer electronics and short-term projects |
If your battery pack is intended for critical applications like medical devices or robotics, pure nickel is the better choice. For less demanding uses, nickel-plated steel may suffice. However, keep in mind that the higher resistance of nickel-plated steel can lead to increased heat generation, which may affect the longevity of your battery pack.
2.3 Calculating current-carrying capacity for optimal performance
The current-carrying capacity of nickel strips determines how much current they can handle without overheating. This capacity depends on the strip’s dimensions, material, and the operating conditions of your battery pack. For instance, a 0.15 mm thick strip can safely carry up to 17 A, while a 0.2 mm thick strip can handle up to 25 A.
The table below provides a quick reference for the optimal current ratings of various nickel strip sizes:
Strip Size | Optimal [A] | Acceptable [A] | Poor [A] |
---|---|---|---|
0.1 mm × 5 mm | < 2.1 | 3.0 | > 4.2 |
0.1 mm × 7 mm | < 3.0 | 4.5 | > 6.0 |
0.15 mm × 7 mm | < 4.7 | 7.0 | > 9.4 |
0.2 mm × 7 mm | < 6.4 | 9.6 | > 12.8 |
0.3 mm × 7 mm | < 10.0 | 15.0 | > 20.0 |
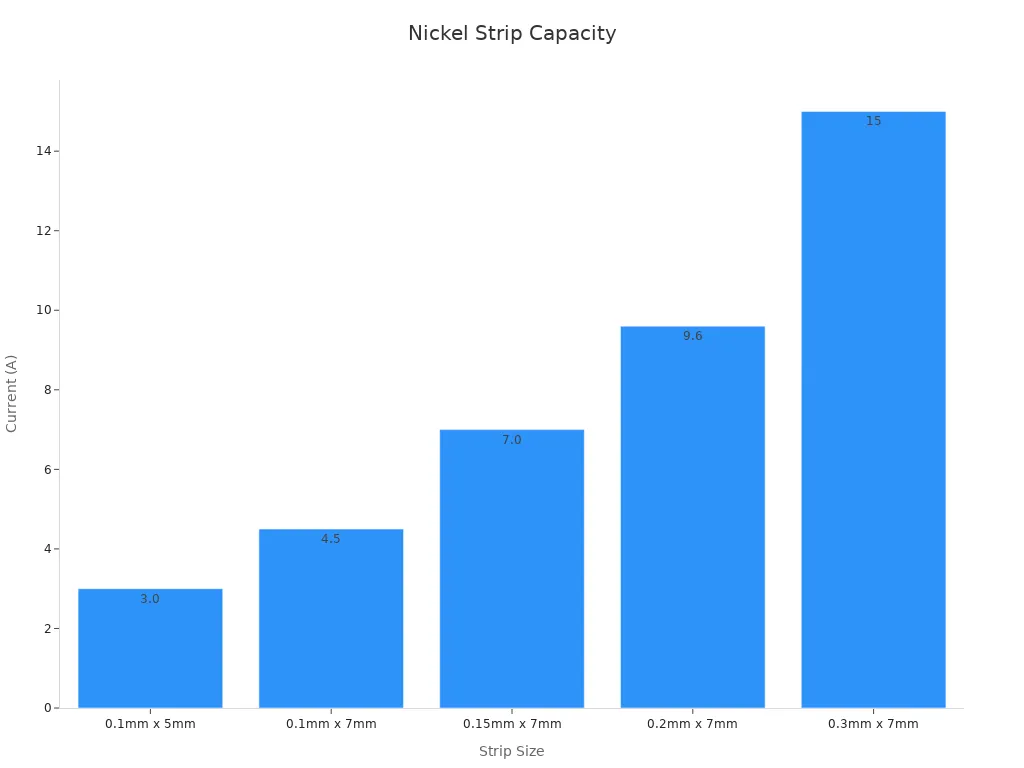
When designing your battery pack, ensure the nickel strips can handle the maximum current output of your BMS. This prevents overheating and ensures the longevity of your lithium-ion battery pack. For more information on BMS operation, visit Battery Management System Operation and Components.
2.4 Matching nickel strips to battery configuration and design
The configuration and design of your battery pack also play a significant role in selecting the right nickel strips. For example, parallel configurations require strips with higher current-carrying capacity, while series configurations benefit from strips with lower resistance to minimize voltage drops.
Consider the following factors when matching nickel strips to your battery design:
Cell Type: Lithium-ion cells, such as NMC or LiFePO4, have different voltage and current requirements. Ensure the nickel strips align with the specific chemistry of your cells.
Pack Size: Larger packs with more cells require wider and thicker strips to handle the increased current load.
Application: High-performance applications like robotics or industrial equipment demand pure nickel strips for reliability and durability.
By carefully matching the nickel strips to your battery’s configuration, you can optimize its performance and ensure safe operation. For custom battery solutions tailored to your specific needs, consult the experts at Large Power.
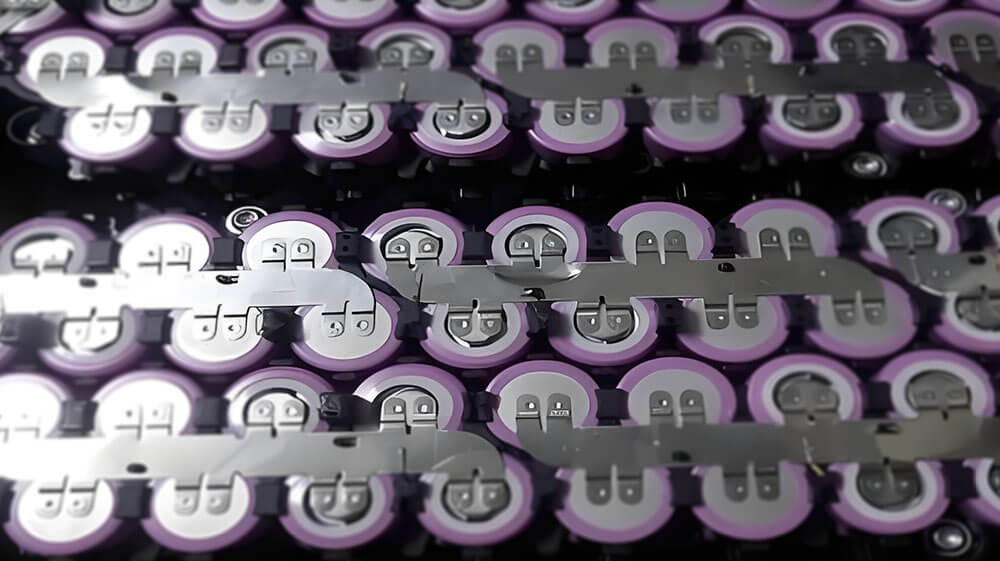
Part 3: Techniques for Soldering Nickel Strips and Other Methods
3.1 Welding vs. soldering: Pros, cons, and best practices
When connecting nickel strips to battery cells, you can choose between welding and soldering. Each method has distinct advantages and limitations, making it essential to select the right approach based on your battery pack’s requirements.
Welding
Welding, particularly spot welding, is the most common method for attaching nickel strips in lithium-ion battery packs. It uses high-current pulses to fuse the strip to the battery terminal, creating a strong and durable bond. This technique minimizes heat transfer to the battery cell, reducing the risk of thermal damage. Spot welding is ideal for high-volume production due to its speed and consistency.
Advantages of Welding:
Produces strong, reliable connections.
Minimizes heat exposure to battery cells.
Suitable for automated processes, ensuring uniformity.
Disadvantages of Welding:
Requires specialized equipment.
Less flexible for intricate or custom designs.
Soldering
Soldering involves melting a filler metal to join the nickel strip to the battery terminal. While it offers greater flexibility for custom or small-scale projects, soldering generates more heat, which can damage lithium-ion cells if not carefully controlled.
Advantages of Soldering:
Allows precise connections, even in complex configurations.
Requires less expensive equipment compared to welding.
Suitable for prototyping and small-scale production.
Disadvantages of Soldering:
Higher risk of heat damage to battery cells.
Time-consuming for large-scale production.
Best Practice: For lithium-ion battery packs, spot welding is generally preferred due to its efficiency and safety. However, soldering remains a viable option for custom or low-volume projects where precision is critical.
3.2 Spot welding: The preferred method for lithium battery packs
Spot welding stands out as the most effective technique for welding nickel strips in lithium battery packs. It ensures a secure connection while preserving the integrity of the battery cells. This method uses a controlled electrical pulse to generate localized heat, fusing the nickel strip to the battery terminal without affecting the surrounding components.
Why Spot Welding is Preferred
Minimal Heat Transfer: Spot welding focuses heat on the connection point, preventing thermal damage to the battery’s internal structure.
High Efficiency: The process is quick, making it ideal for large-scale production.
Consistency: Automated spot welding machines deliver uniform results, reducing the risk of weak connections.
Key Considerations for Spot Welding
Use pure nickel strips for better conductivity and durability.
Ensure the welding machine is calibrated to the correct settings for your strip’s thickness and material.
Test the weld strength regularly to maintain quality standards.
For applications requiring high reliability, such as medical devices or robotics, spot welding provides the durability and precision needed to meet industry demands. Learn more about sustainable battery solutions at Sustainability at Large Power.
3.3 Tips for achieving strong and reliable connections
Creating strong and reliable connections is crucial for the performance and safety of your battery pack. Whether you choose welding or soldering, following these tips can help you achieve optimal results:
Use High-Quality Materials: Always opt for pure nickel strips to ensure better conductivity and resistance to corrosion.
Maintain Clean Surfaces: Before welding or soldering, clean the battery terminals and nickel strips to remove any dirt or oxidation that could weaken the connection.
Monitor Heat Levels: Excessive heat can damage lithium-ion cells. Use precise tools to control the temperature during soldering or welding.
Employ Skilled Technicians: Hand soldering by skilled professionals allows for precise connections, especially in intricate designs. Technicians can adjust the process in real-time to maintain quality.
Utilize Proper Tools: For crimped connections, use a precise crimping tool to ensure uniformity and durability. Crimped connections are particularly resistant to vibrations and mechanical stress.
Pro Tip: Regularly inspect your connections for signs of wear or corrosion. Early detection of issues can prevent performance degradation and extend the lifespan of your battery pack.
By implementing these effective techniques for welding and soldering, you can enhance the reliability and safety of your battery packs. For custom battery solutions tailored to your specific needs, consult the experts at Large Power.
Part 4: Common Problems with Nickel Strips for Battery Packs
4.1 Overheating and its impact on battery performance
Overheating is one of the most critical issues in battery pack construction. When nickel strips are undersized or poorly connected, they generate excessive heat during operation. This heat can damage the lithium-ion cells, reducing their lifespan and increasing the risk of thermal runaway. For instance, a strip with insufficient thickness may struggle to handle high current loads, leading to localized heating.
To mitigate overheating, you should always calculate the current-carrying capacity of the nickel strips based on your battery pack’s design. Using thicker or wider strips can help distribute the current more effectively, minimizing heat buildup. Additionally, ensure proper ventilation and thermal management within the battery pack to maintain safe operating temperatures.
Tip: Regularly monitor the temperature of your battery pack during operation. Early detection of overheating can prevent severe damage and improve overall safety.
4.2 Identifying and fixing poor connections
Poor connections between nickel strips and battery cells can lead to uneven energy transfer and increased resistance. This issue often arises from improper welding or soldering techniques. Signs of poor connections include voltage drops, inconsistent performance, and visible gaps between the strip and the cell.
To fix this, inspect all connections during the battery pack construction process. Use spot welding for a secure and reliable bond, as it minimizes heat exposure to the cells. If soldering is necessary, ensure the use of high-quality solder and precise temperature control to avoid damaging the cells.
4.3 Preventing material degradation and corrosion
Material degradation and corrosion can compromise the performance and safety of nickel strips over time. Factors such as humidity, temperature fluctuations, and exposure to corrosive environments accelerate this process. Research on nickel and nickel-copper nanolaminates highlights how surface imperfections can initiate localized corrosion, reducing the long-term integrity of the strips.
Key Findings | Description |
---|---|
Hot Corrosion Behavior | Observed at 900 °C, showing distinct characteristics post-drilling. |
Stable Oxide Layer | Formation reduces spalling effects, enhancing durability. |
Microstructure Changes | Altered diffusion processes improve corrosion resistance. |
To prevent corrosion, use pure nickel strips, as they offer superior resistance compared to nickel-plated steel. Additionally, store and operate your battery packs in controlled environments to minimize exposure to moisture and contaminants.
4.4 Short circuits and electrical hazards
Short circuits pose significant risks in battery pack construction. They can occur when nickel strips come into contact with unintended components, creating a direct path for current flow. This can lead to overheating, cell damage, or even fire hazards.
To prevent short circuits, ensure proper insulation between nickel strips and other conductive parts. Use heat-resistant materials to separate layers within the battery pack. Additionally, inspect the pack for any loose or frayed connections that could cause accidental contact.
Pro Tip: Incorporate a Battery Management System (BMS) to monitor and regulate the electrical flow within your battery pack. A BMS can detect and address potential short circuits before they escalate.
By addressing these common problems, you can enhance the reliability and safety of your battery packs. For custom solutions tailored to your specific needs, consult the experts at Large Power.
Proper sizing and selection of nickel strips are essential for optimizing the performance and safety of lithium-ion battery packs. Applying the techniques shared in this guide ensures reliable energy transfer and durability. For complex projects or custom solutions, consult the experts at Large Power to achieve tailored results.
FAQ
1. What is the best material for nickel strips in lithium-ion battery packs?
Pure nickel is ideal due to its high conductivity and corrosion resistance. It ensures durability and efficiency, especially for critical applications like robotics and medical devices.
2. How do I calculate the required thickness of nickel strips?
Use the formula:Resistance = Length / (Width × Thickness) × Bulk Resistivity
.
This ensures the strip can handle the current without overheating. Consult Large Power for expert guidance.
3. Can nickel strips be used in industrial battery applications?
Yes, nickel strips are suitable for industrial applications due to their durability and ability to handle high currents. Pure nickel is recommended for long-term reliability.